Metodele de acoperire ale fotorezistului sunt, în general, împărțite în acoperire prin centrifugare, acoperire prin scufundare și acoperire cu rolă, dintre care acoperirea prin rotație este cea mai frecvent utilizată. Prin acoperire prin rotație, fotorezistul este picurat pe substrat, iar substratul poate fi rotit la viteză mare pentru a obține un film de fotorezist. După aceea, o peliculă solidă poate fi obținută prin încălzirea acesteia pe o placă fierbinte. Acoperirea prin rotire este potrivită pentru acoperirea de la filme ultra-subțiri (aproximativ 20 nm) la filme groase de aproximativ 100um. Caracteristicile sale sunt uniformitatea bună, grosimea uniformă a filmului între plachete, puține defecte etc. și se poate obține o peliculă cu performanță ridicată de acoperire.
Proces de acoperire prin centrifugare
În timpul acoperirii prin centrifugare, viteza principală de rotație a substratului determină grosimea filmului de fotorezist. Relația dintre viteza de rotație și grosimea filmului este următoarea:
Spin=kTn
În formulă, Spin este viteza de rotație; T este grosimea peliculei; k și n sunt constante.
Factori care afectează procesul de acoperire prin centrifugare
Deși grosimea filmului este determinată de viteza principală de rotație, aceasta este, de asemenea, legată de temperatura camerei, umiditate, vâscozitatea fotorezist și tipul de fotorezist. Comparația diferitelor tipuri de curbe de acoperire fotorezistentă este prezentată în Figura 1.
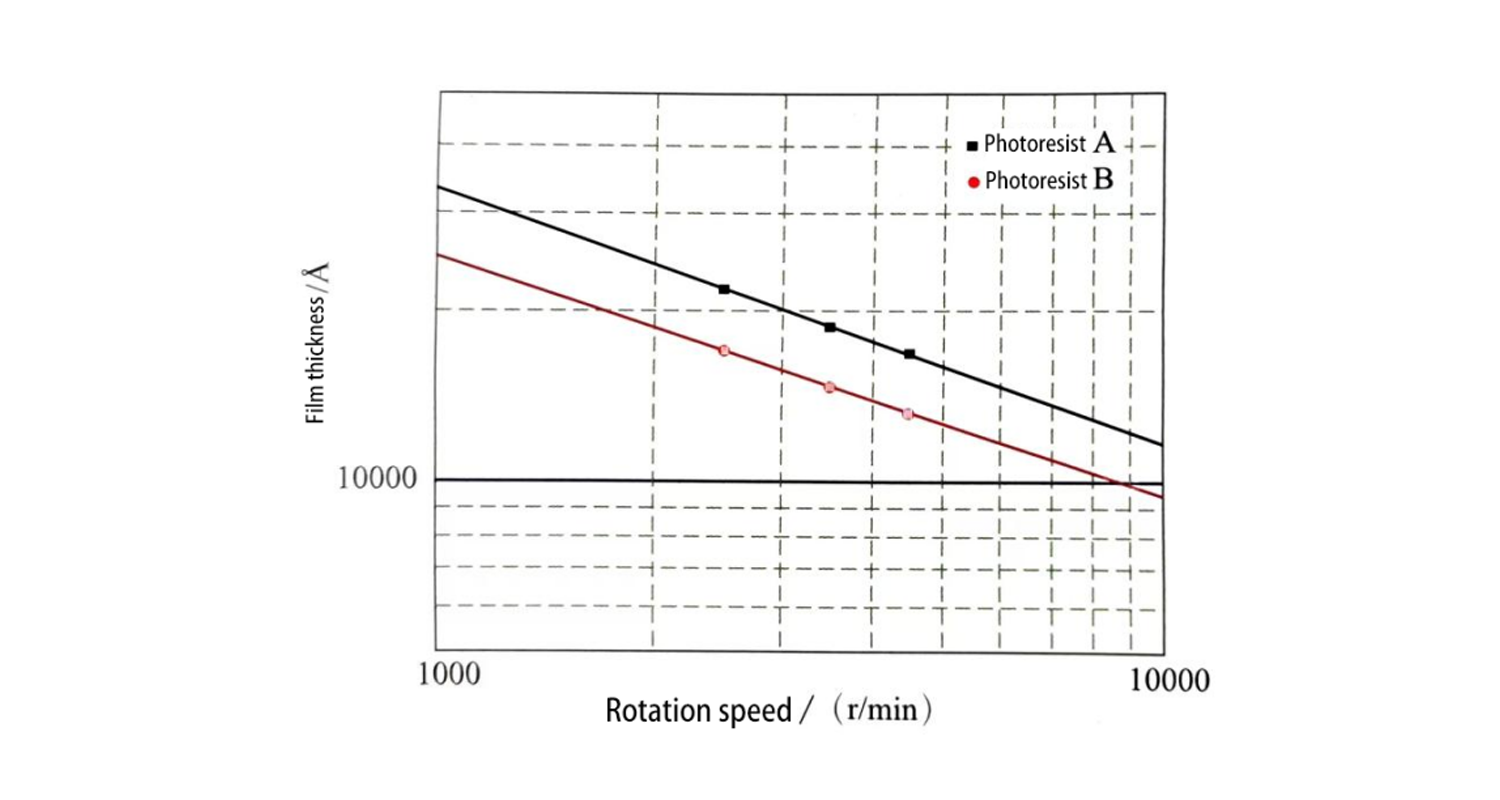
Figura 1: Comparația diferitelor tipuri de curbe de acoperire cu fotorezist
Influența timpului de rotație principală
Cu cât timpul de rotație principal este mai scurt, cu atât grosimea filmului este mai groasă. Când timpul de rotație principal este crescut, cu atât filmul devine mai subțire. Când depășește 20 de secunde, grosimea filmului rămâne aproape neschimbată. Prin urmare, timpul de rotație principal este de obicei selectat să fie mai mare de 20 de secunde. Relația dintre timpul de rotație principal și grosimea filmului este prezentată în Figura 2.
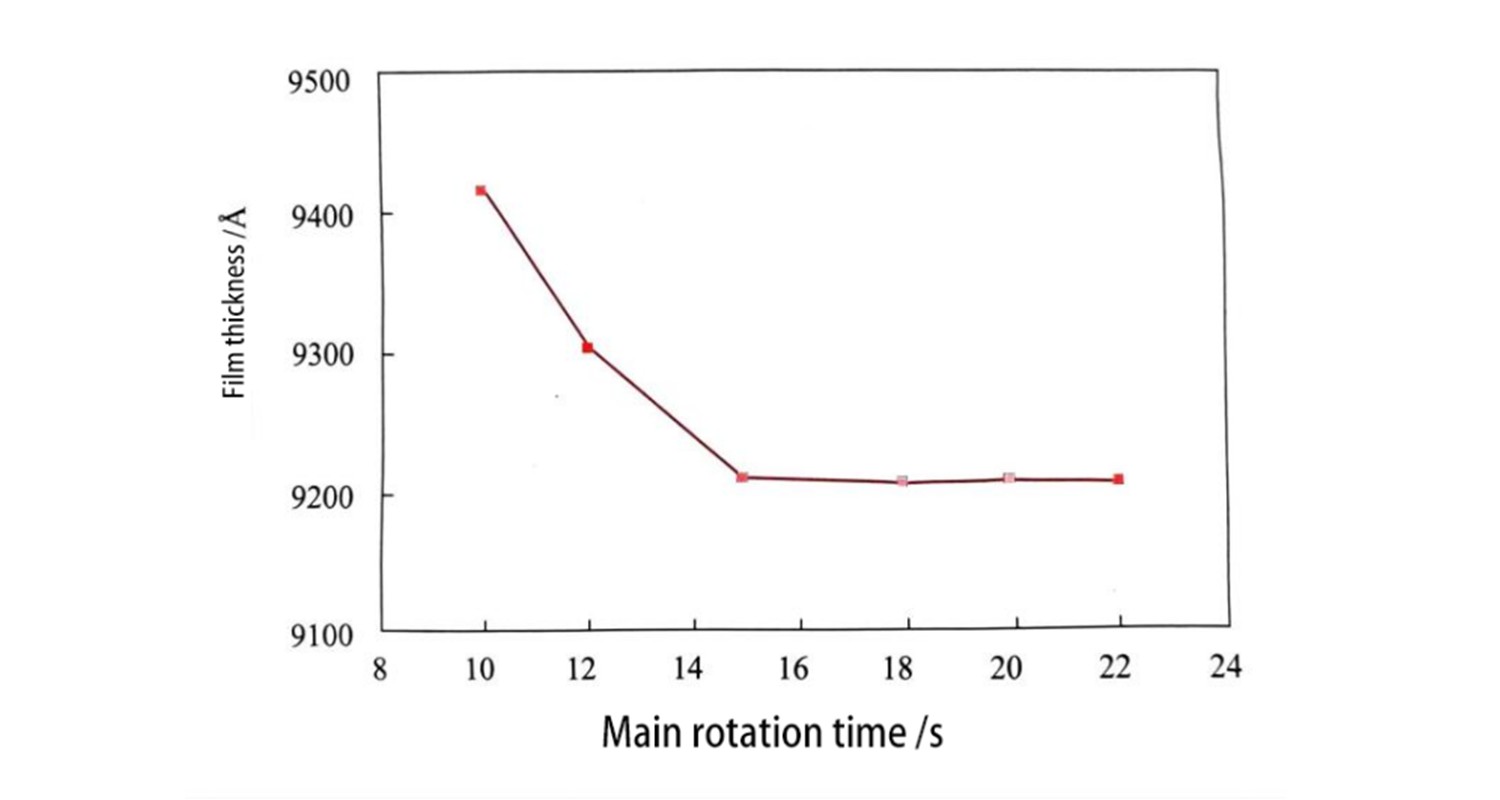
Figura 2: Relația dintre timpul de rotație principal și grosimea filmului
Când fotorezistul este picurat pe substrat, chiar dacă viteza de rotație principală ulterioară este aceeași, viteza de rotație a substratului în timpul picurarii va afecta grosimea finală a filmului. Grosimea filmului de fotorezist crește odată cu creșterea vitezei de rotație a substratului în timpul picurarii, ceea ce se datorează influenței evaporării solventului atunci când fotorezistul este desfășurat după picurare. Figura 3 arată relația dintre grosimea filmului și viteza principală de rotație la diferite viteze de rotație a substratului în timpul picurarii fotorezist. Se poate observa din figură că odată cu creșterea vitezei de rotație a substratului de picurare, grosimea filmului se modifică mai repede, iar diferența este mai evidentă în zona cu viteză principală de rotație mai mică.
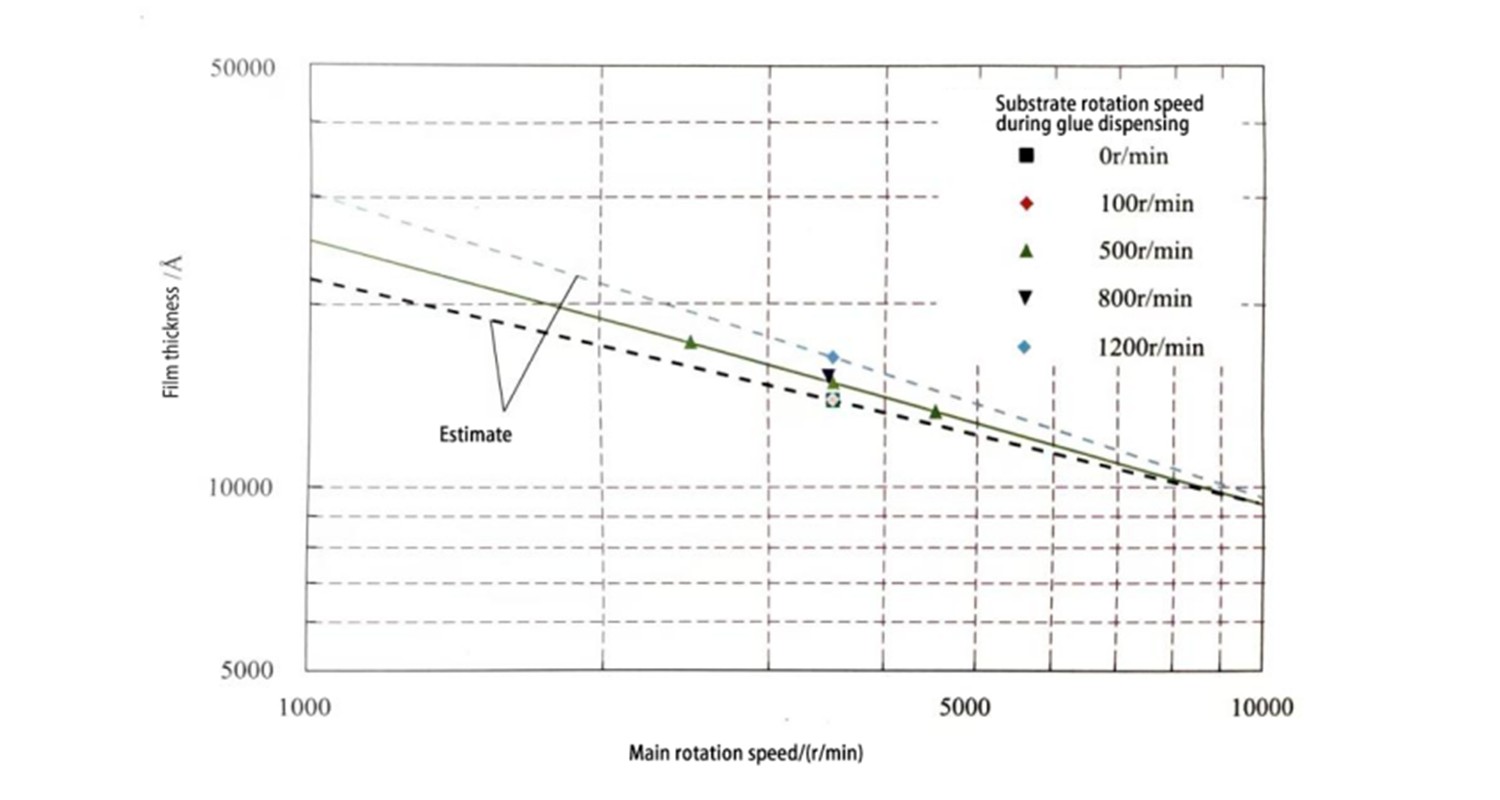
Figura 3: Relația dintre grosimea filmului și viteza de rotație principală la diferite viteze de rotație a substratului în timpul distribuirii de fotorezist
Efectul umidității în timpul acoperirii
Când umiditatea scade, grosimea peliculei crește, deoarece scăderea umidității favorizează evaporarea solventului. Cu toate acestea, distribuția grosimii filmului nu se modifică semnificativ. Figura 4 arată relația dintre umiditate și distribuția grosimii filmului în timpul acoperirii.
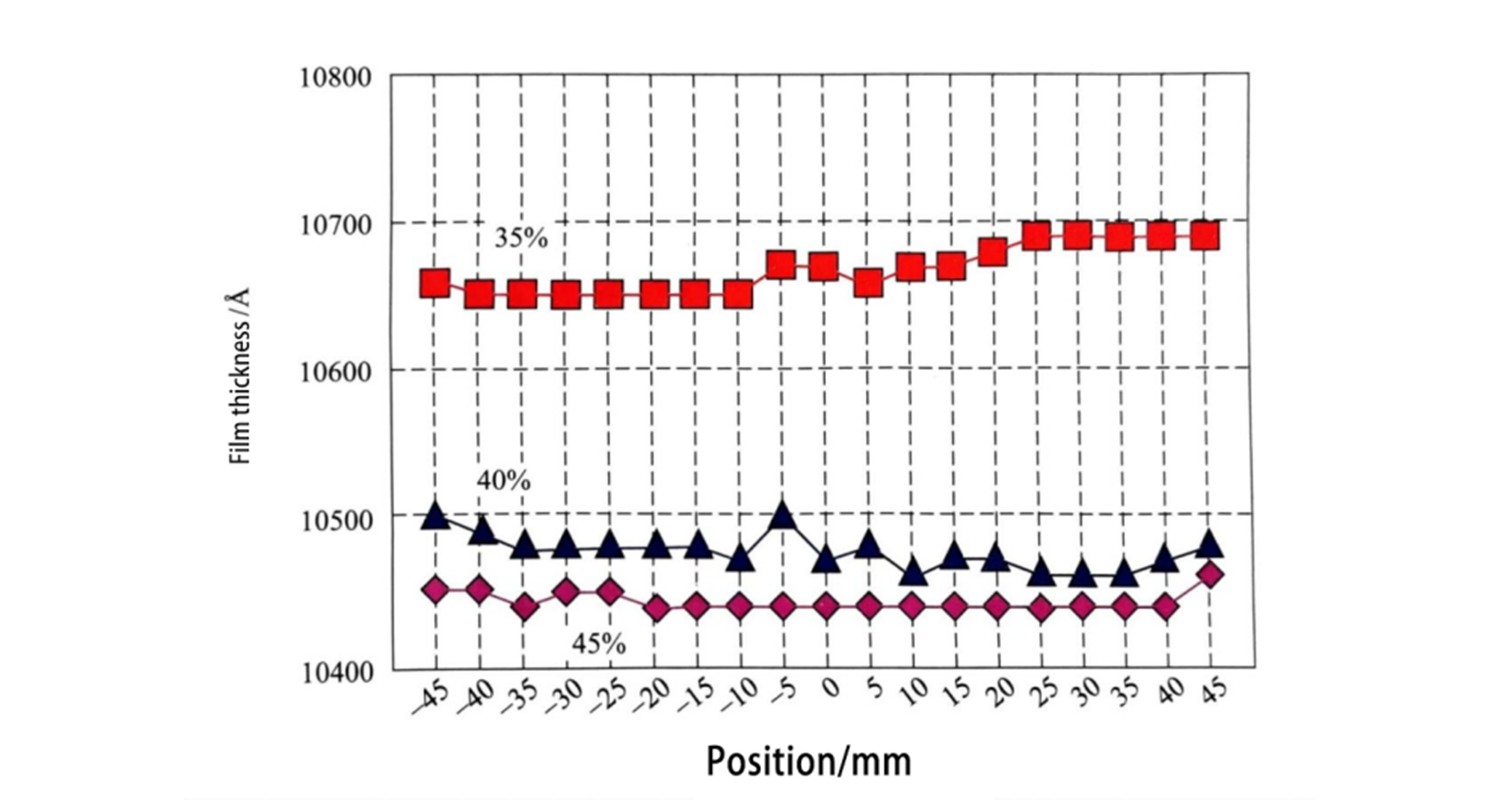
Figura 4: Relația dintre umiditate și distribuția grosimii filmului în timpul acoperirii
Efectul temperaturii în timpul acoperirii
Când temperatura interioară crește, grosimea filmului crește. Din figura 5 se poate observa că distribuția grosimii filmului fotorezist se schimbă de la convex la concav. Curba din figură arată, de asemenea, că cea mai mare uniformitate se obține atunci când temperatura interioară este de 26°C și temperatura fotorezist este de 21°C.
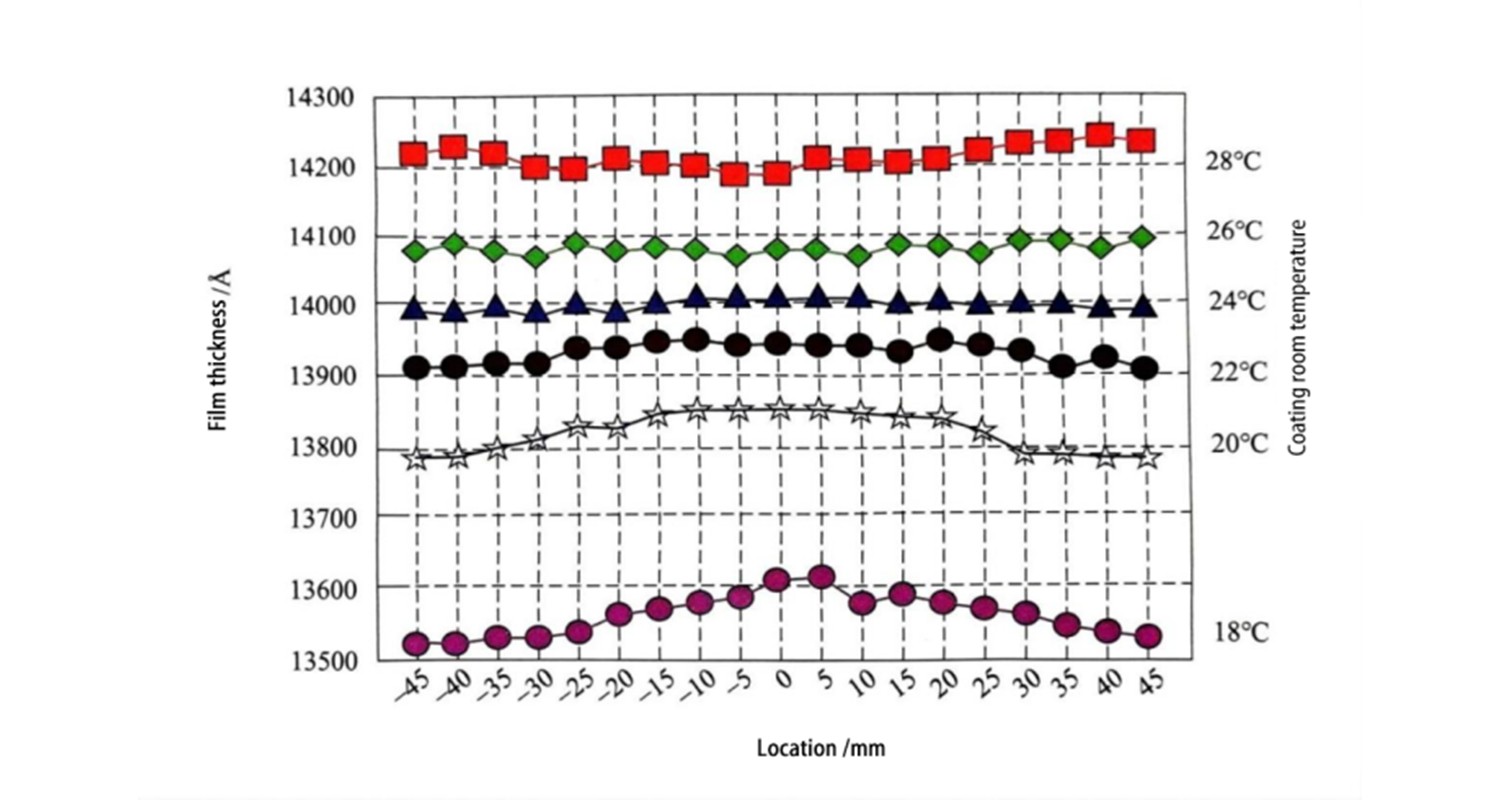
Figura 5: Relația dintre temperatură și distribuția grosimii filmului în timpul acoperirii
Efectul vitezei de evacuare în timpul acoperirii
Figura 6 arată relația dintre viteza de evacuare și distribuția grosimii filmului. În absența eșapamentului, arată că centrul plachetei tinde să se îngroașe. Creșterea vitezei de evacuare va îmbunătăți uniformitatea, dar dacă este mărită prea mult, uniformitatea va scădea. Se poate observa că există o valoare optimă pentru viteza de evacuare.
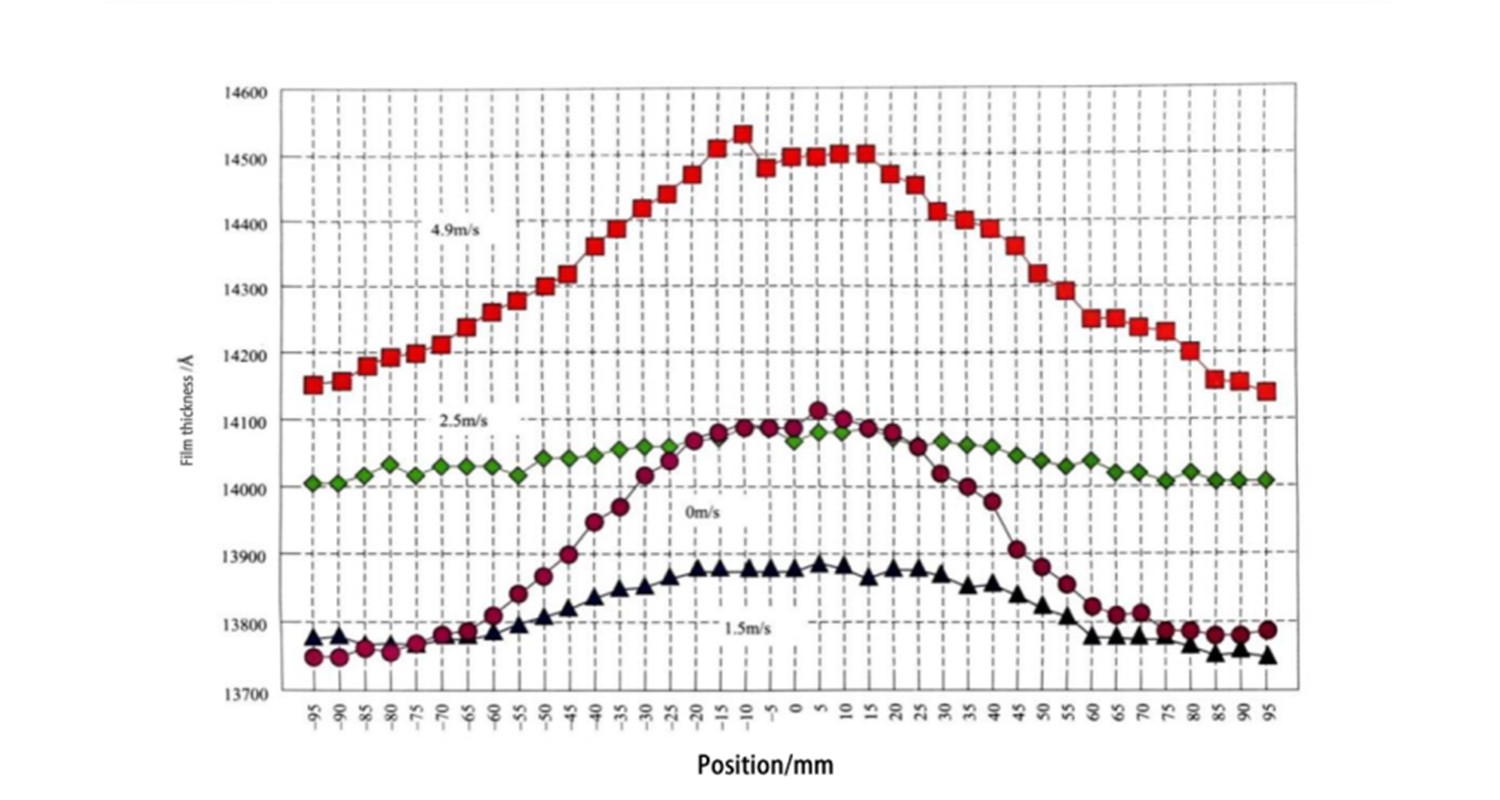
Figura 6: Relația dintre viteza de evacuare și distribuția grosimii filmului
Tratamentul HMDS
Pentru a face fotorezistul mai acoperibil, napolitana trebuie tratată cu hexametildisilazan (HMDS). În special atunci când umiditatea este atașată la suprafața filmului de oxid de Si, se formează silanol, ceea ce reduce aderența fotorezistului. Pentru a îndepărta umezeala și a descompune silanolul, napolitana este de obicei încălzită la 100-120°C și se introduce ceața HMDS pentru a provoca o reacție chimică. Mecanismul de reacție este prezentat în Figura 7. Prin tratamentul HMDS, suprafața hidrofilă cu un unghi de contact mic devine o suprafață hidrofobă cu un unghi de contact mare. Încălzirea plachetei poate obține o aderență mai mare a fotorezistului.
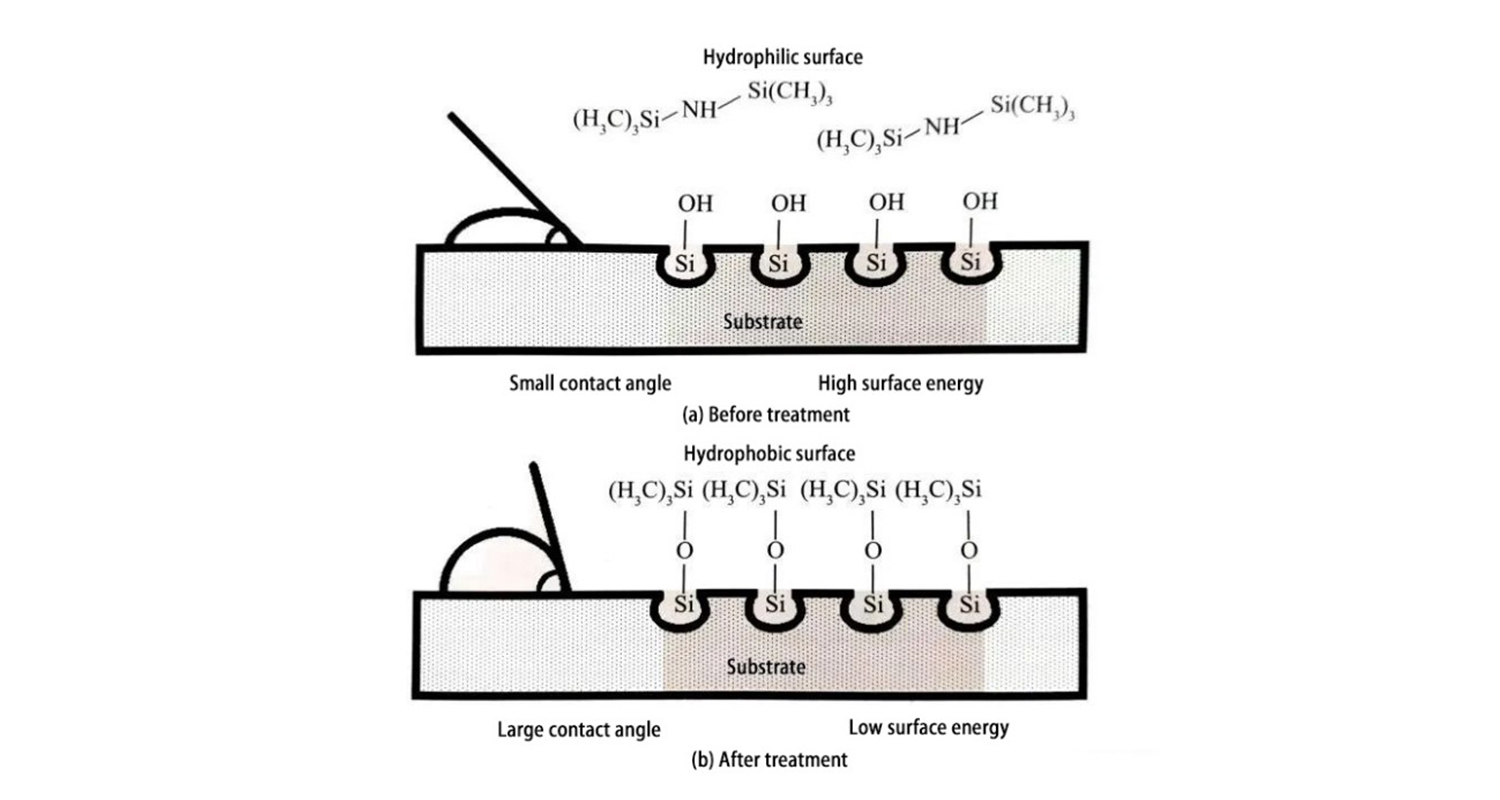
Figura 7: Mecanismul de reacție HMDS
Efectul tratamentului cu HMDS poate fi observat prin măsurarea unghiului de contact. Figura 8 prezintă relația dintre timpul de tratament HMDS și unghiul de contact (temperatura de tratament 110°C). Substratul este Si, timpul de tratament HMDS este mai mare de 1 min, unghiul de contact este mai mare de 80°, iar efectul tratamentului este stabil. Figura 9 prezintă relația dintre temperatura de tratament HMDS și unghiul de contact (timp de tratament 60s). Când temperatura depășește 120℃, unghiul de contact scade, indicând faptul că HMDS se descompune din cauza căldurii. Prin urmare, tratamentul cu HMDS se efectuează de obicei la 100-110 ℃.
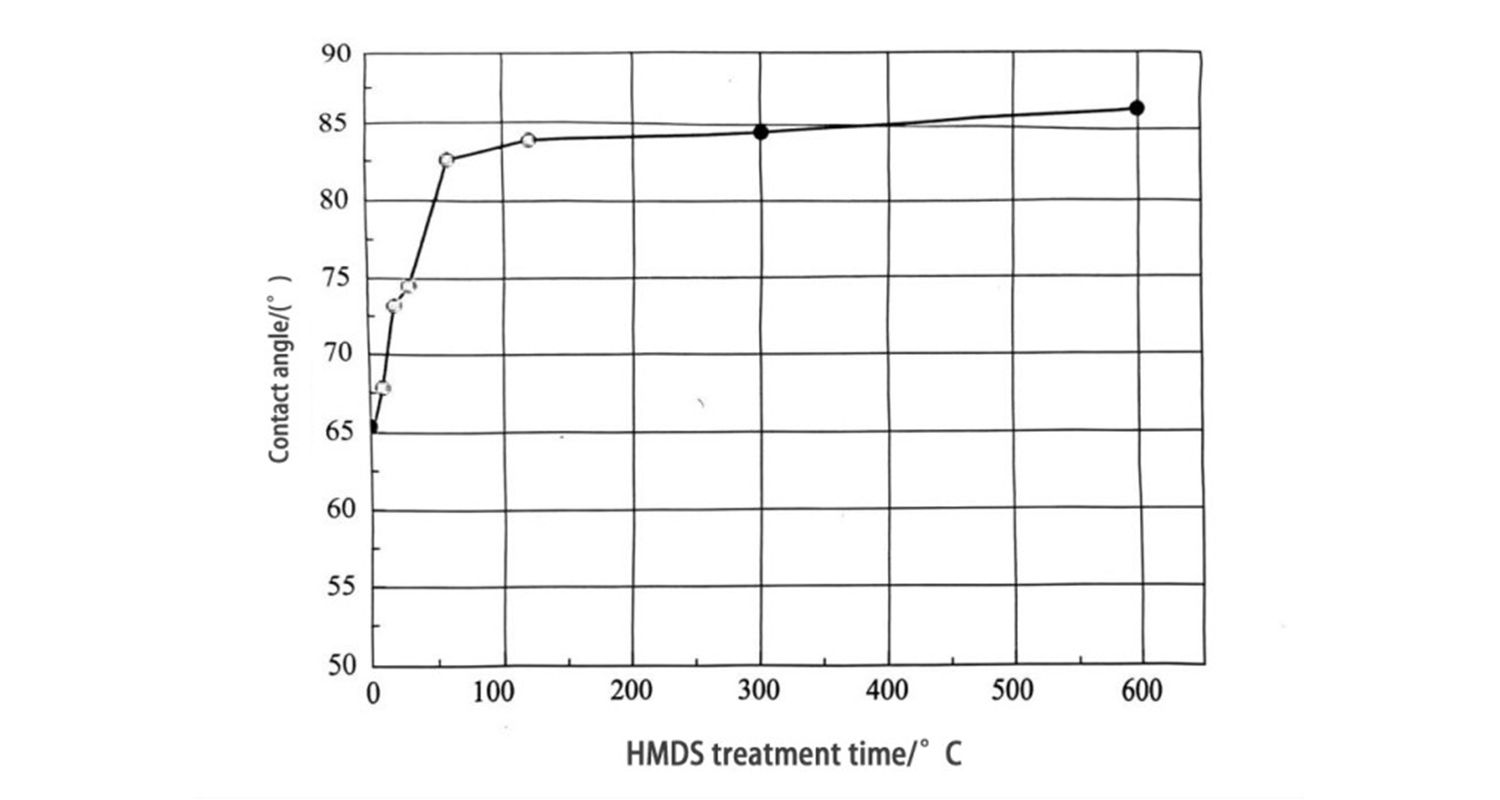
Figura 8: Relația dintre timpul de tratament HMDS
și unghiul de contact (temperatura de tratament 110℃)
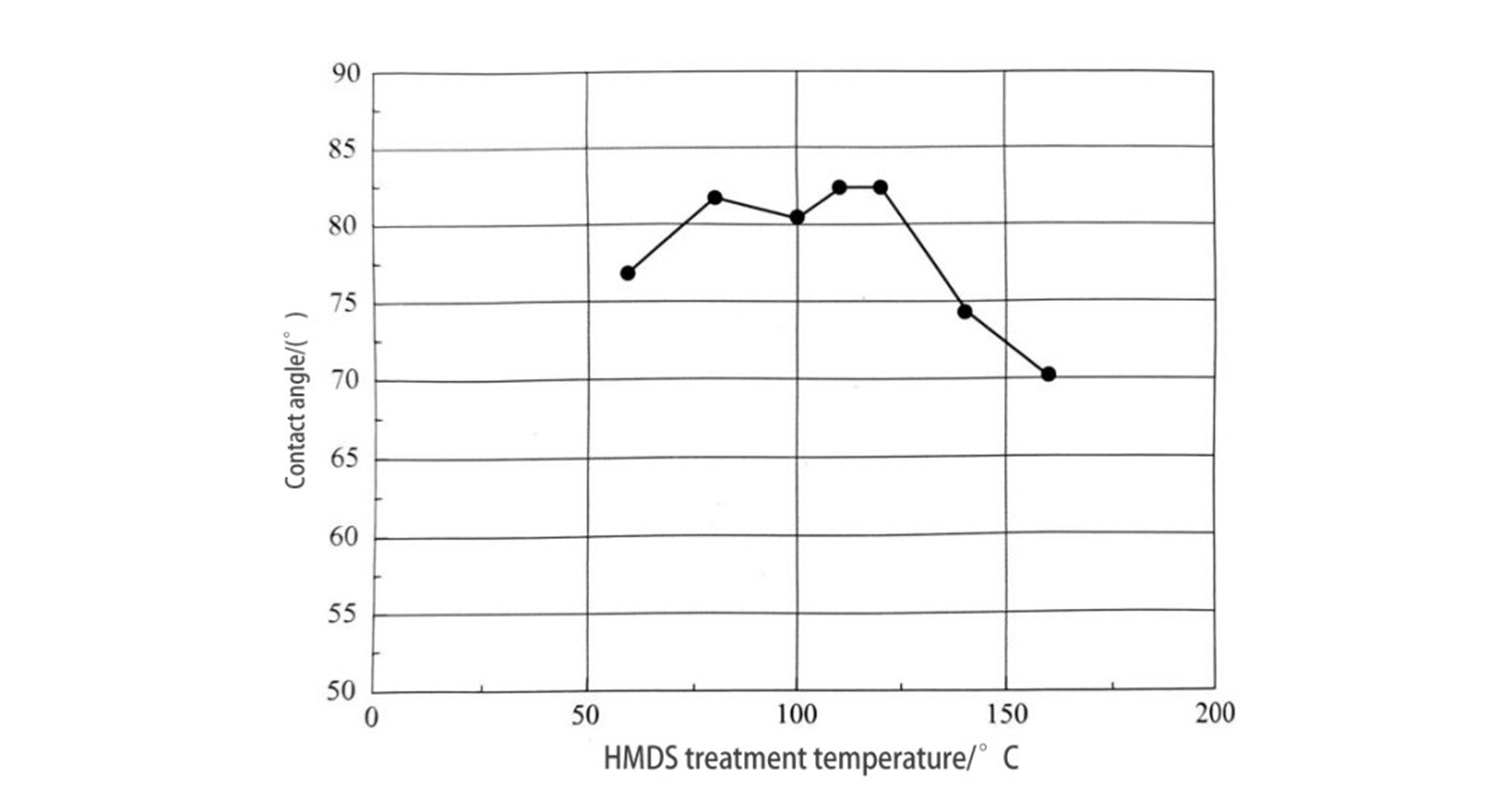
Figura 9: Relația dintre temperatura de tratament HMDS și unghiul de contact (timp de tratament 60s)
Tratamentul HMDS este efectuat pe un substrat de siliciu cu o peliculă de oxid pentru a forma un model fotorezistent. Filmul de oxid este apoi gravat cu acid fluorhidric cu un tampon adăugat și se constată că după tratamentul cu HMDS, modelul fotorezist poate fi împiedicat să cadă. Figura 10 arată efectul tratamentului cu HMDS (dimensiunea modelului este de 1um).
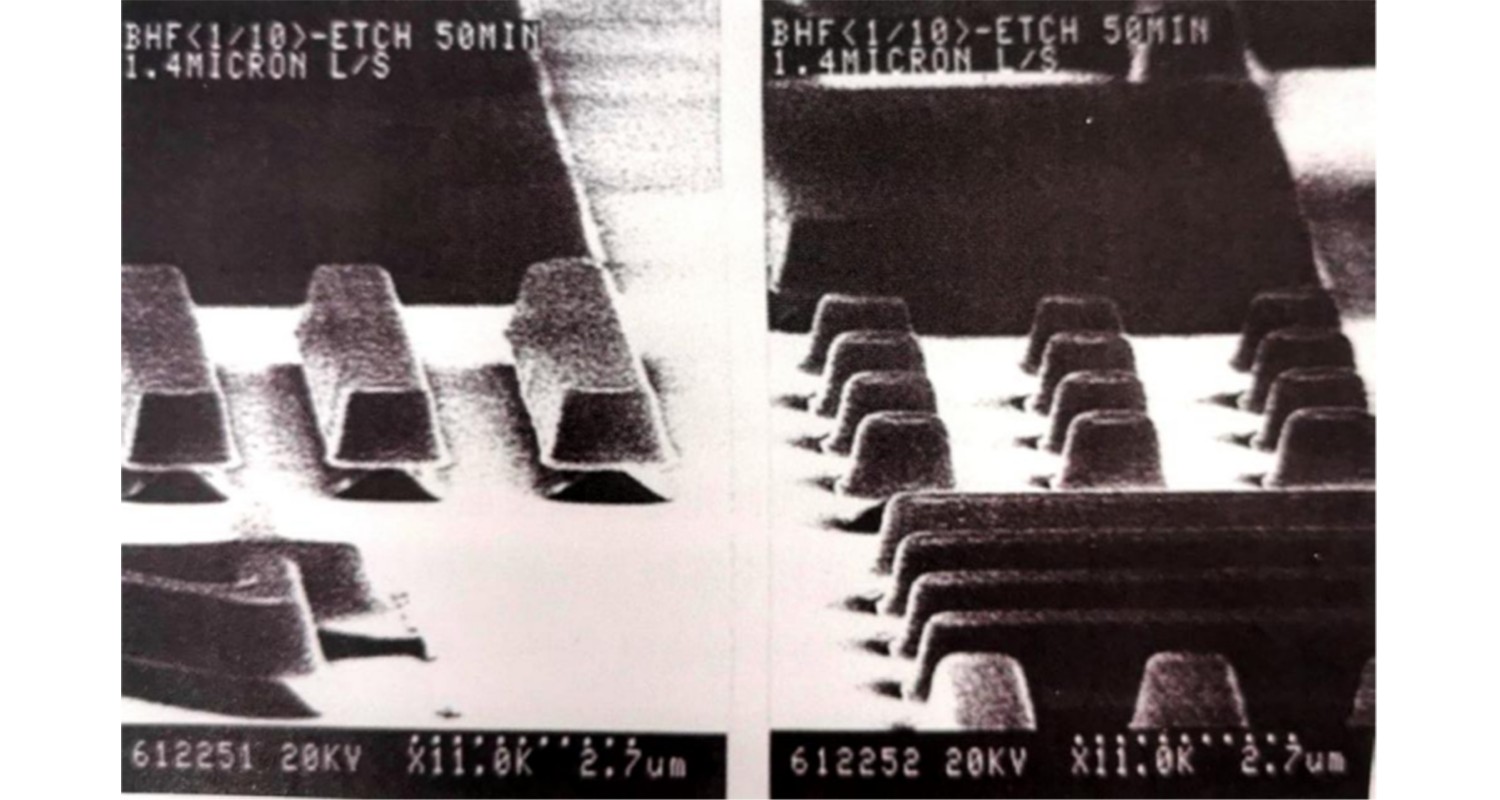
Figura 10: Efectul tratamentului HMDS (dimensiunea modelului este de 1um)
Precoacerea
La aceeași viteză de rotație, cu cât temperatura de precocere este mai mare, cu atât grosimea filmului este mai mică, ceea ce indică faptul că cu cât temperatura de precocere este mai mare, cu atât se evaporă mai mult solvent, rezultând o grosime mai subțire a peliculei. Figura 11 arată relația dintre temperatura de pre-cocere și parametrul A al mărarului. Parametrul A indică concentrația agentului fotosensibil. După cum se poate observa din figură, atunci când temperatura de pre-cocere crește la peste 140°C, parametrul A scade, indicând faptul că agentul fotosensibil se descompune la o temperatură mai mare decât aceasta. Figura 12 prezintă transmisia spectrală la diferite temperaturi de pre-cocere. La 160°C și 180°C, se poate observa o creștere a transmitanței în intervalul de lungimi de undă de 300-500nm. Acest lucru confirmă faptul că agentul fotosensibil este copt și descompus la temperaturi ridicate. Temperatura de pre-cocere are o valoare optimă, care este determinată de caracteristicile luminii și de sensibilitate.
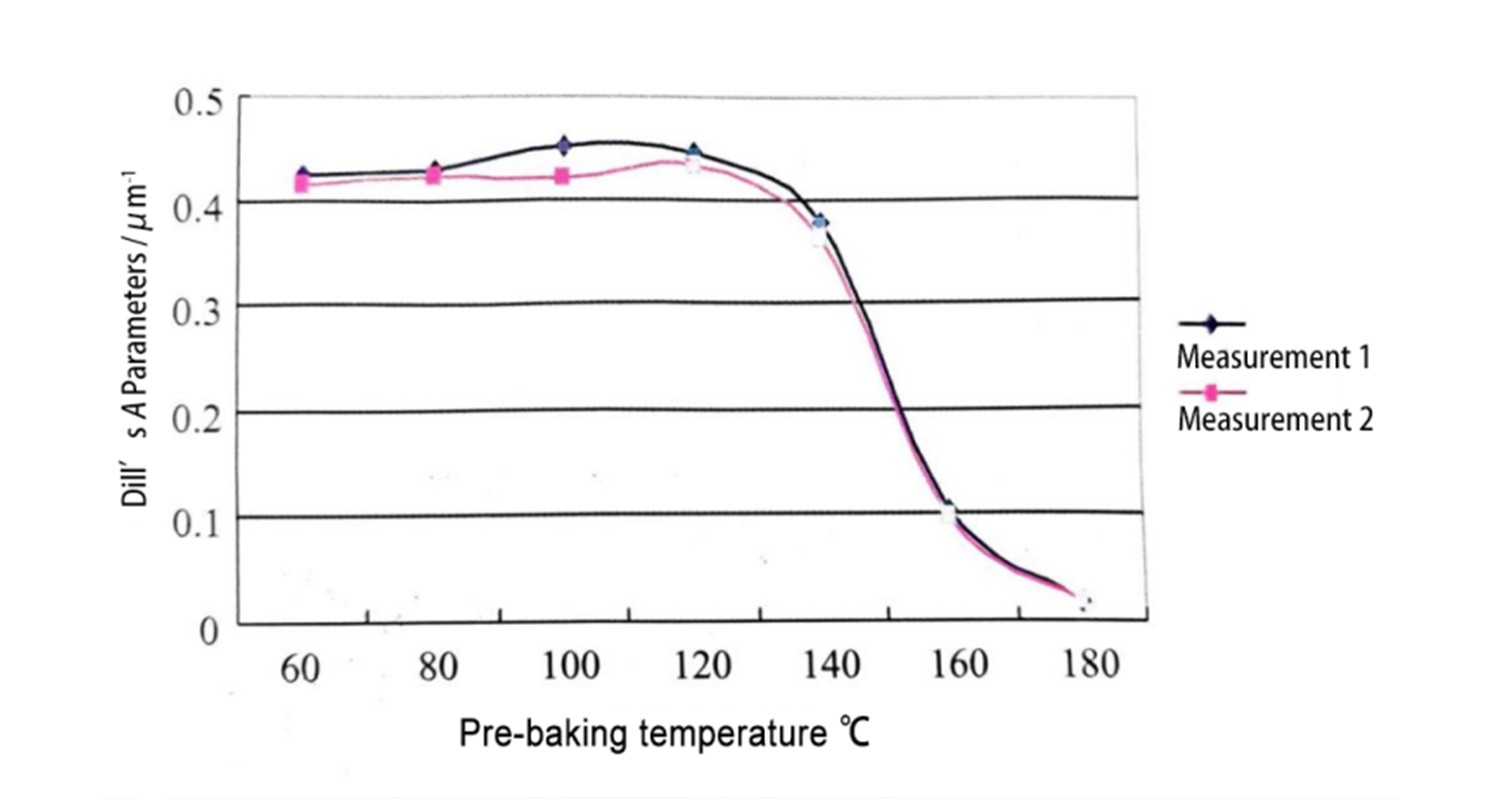
Figura 11: Relația dintre temperatura înainte de coacere și parametrul Mararului A
(valoarea măsurată a OFPR-800/2)
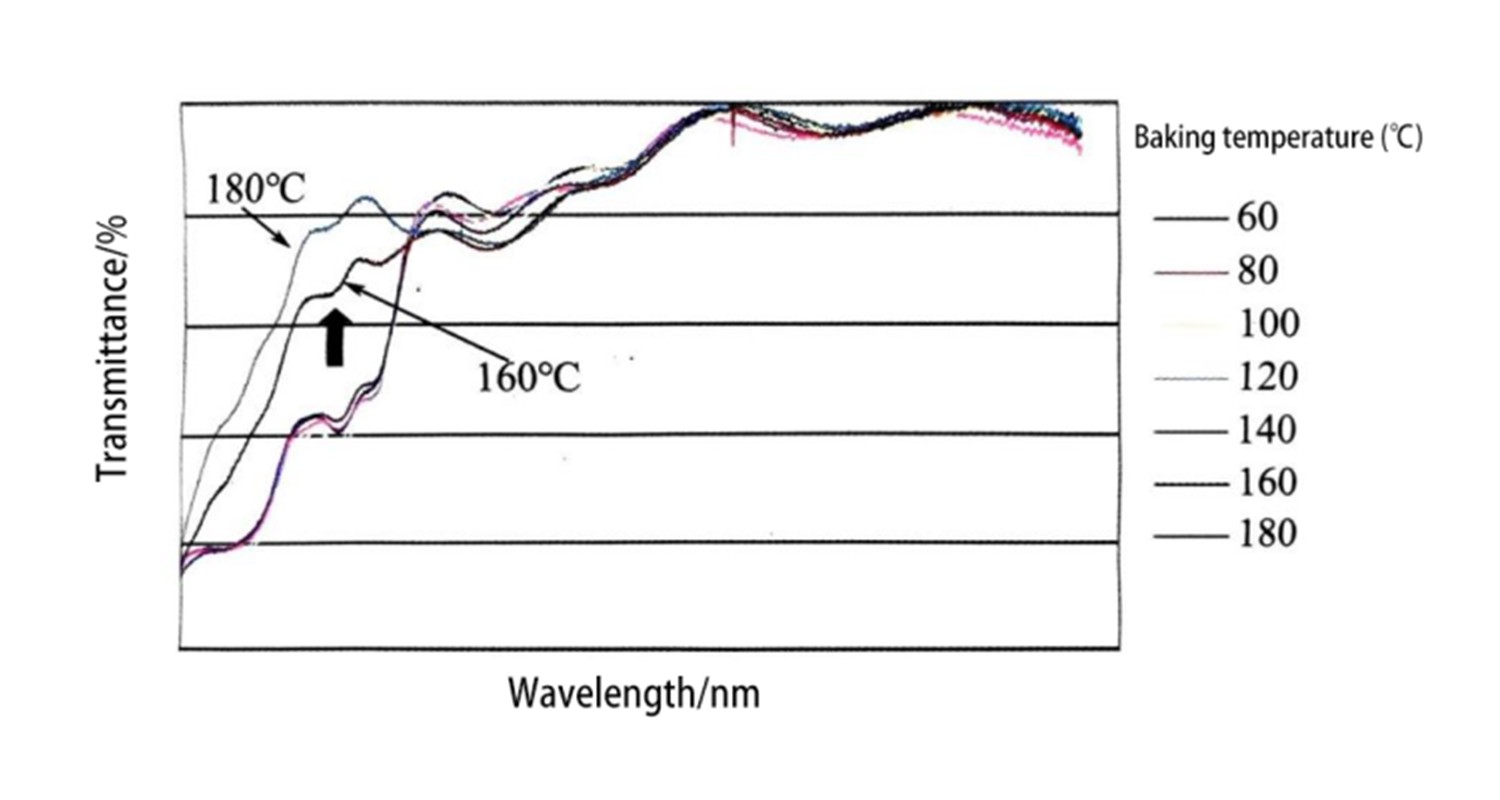
Figura 12: Transmitanța spectrală la diferite temperaturi înainte de coacere
(OFPR-800, grosime film de 1um)
Pe scurt, metoda de acoperire prin centrifugare are avantaje unice, cum ar fi controlul precis al grosimii filmului, performanța la costuri ridicate, condițiile de proces ușoare și operarea simplă, astfel încât are efecte semnificative în reducerea poluării, economisirea energiei și îmbunătățirea performanței costurilor. În ultimii ani, acoperirea prin spin a câștigat o atenție din ce în ce mai mare, iar aplicarea sa s-a extins treptat în diverse domenii.
Ora postării: 27-nov-2024